A Guide to Static Elimination – Basic Rules and Principles
There are rules in static elimination which must be followed. A thorough understanding of these principles is essential to getting the best performance out of your equipment. The following will shed some light on the issues to be considered when specifying the type and location of a static eliminator.
Distance from the Object to be Neutralised
AC ionisation does not have a long life. It recombines quickly, so ‘the closer, the better’.
- The performance of a 1250 Static Eliminator bar is six times better at 25 mm than it is at 50 mm
- The performance of a 2010 Ionised Air Blower is nearly three times better at 500 mm than at 1 m
DC ionisation has a longer life than AC ionisation, but DC equipment must still be positioned as close to the object as possible. For any given static eliminator bar type, the single factor having the greatest influence over performance is distance to target.
- For instance, the 3024L Static Eliminator is nearly 3 times as powerful at 200 mm than at 300 mm and almost as effective at 200 mm compared to a NEOS 30 at 400 mm.
Note:
For long-range, high-performance bars, to allow the ionisation to cover the whole object, we do not recommend positioning the bar closer than 250 mm.
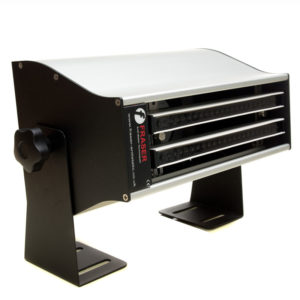
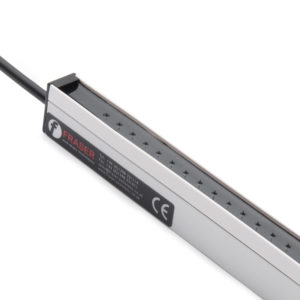
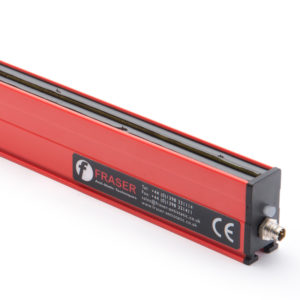
Material must be in Free Air
If a film is touching a roller, for example, you cannot neutralise the charge with static eliminators at that point. This causes the most common mistake in our industry. When the charged material is touching another body, the electric field couples with that body and is not available for neutralisation (or measurement). You must wait until the material has separated from that body.
This also applies to three-dimensional products such as mouldings. A flat moulding sliding down a chute, or on a conveyor, cannot be neutralised. There may be some static elimination, depending how tall the product is. The part touching the chute will not be neutralised, the part furthest from the chute will be partly neutralised. Neutralisation depends on the capacitance of the product.
A partial exception to this is with pulsed-DC static elimination equipment. DC (direct current) ionisation has more ability to neutralise charge which is coupled with another body. This is because DC can flow through the object, unlike AC. However, this is only a partial exception and the general rule still applies: neutralisation is best if the product is in free air.
We recommend that there is at least 50 mm between the contact point with the roller and the location of the neutralisation.
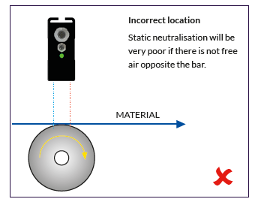
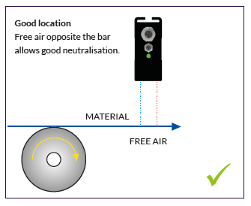
Neutralise Immediately Before the Problem
There may be several positions in a process where static may be generated. If you neutralise the static too early, it could regenerate as it passes over rollers or through other processes. So, position the static eliminator to neutralise the material at the last possible position before the problem area.
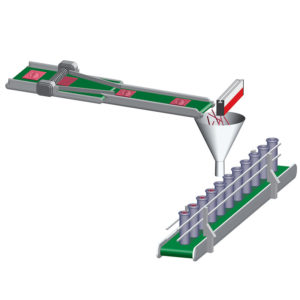
Dust and Static
Statically attracted dust must be removed as soon as possible after attraction. If dusty mouldings are stored for a few days, the electrostatic attraction can be replaced by a molecular bonding. When this happens, the product cannot be cleaned by neutralising the static charge and blowing-off the dust - the product needs to be wiped with a wet cloth or with solvents. The lesson here is to neutralise the charge and remove the dust immediately after attraction. This is important in the injection moulding industry, where mouldings are to be painted. Neutralisation may be needed after moulding and again after de-flashing.
The Material in Free Air rule explained earlier also applies to cleaning with ionised air guns. You cannot completely neutralise a plastic sheet if it is lying flat on a table. This means that it may be able to re-attract dust after cleaning when it is removed from the table.
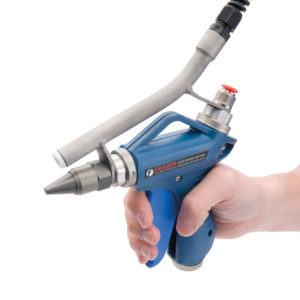
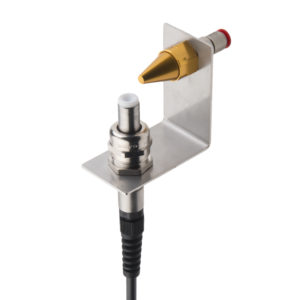
Heat and Static
A plastic product is not electrically stable until it is relatively cool, 40 ºC – 50 ºC is a typical target figure for electrical stability. The significance of this is that it is possible for a hot moulding to regenerate some of the charge after neutralisation if it is still hot. This argues that static neutralisation should wait until the moulding has cooled to 40 ºC before neutralisation.
However, the argument for neutralising the moulding as soon as possible is that it will prevent dust attraction from occurring. We often install small ionised air nozzles on robot arms to neutralise the moulding as soon as it is picked up. Using an ionised air nozzle or blower is beneficial as it helps cool the moulding as well as neutralise the static charge.
A secondary static eliminator may be necessary if the static charge is regenerated in cooling.
Speed of the Material
Static generation is proportional to the speed of the material. Faster speeds create higher charges. The speed of the material also determines whether more than one static eliminator bar is required. Some years ago, the rule was that if the material speed was over 300 m/min then 2 or more AC static eliminators were required. Modern pulsed DC static eliminators are more powerful and can cope with higher speeds. Even so, more than one bar may be required - especially if the charge level is high.
Passive static eliminators do not have a speed restriction.
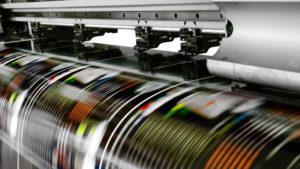
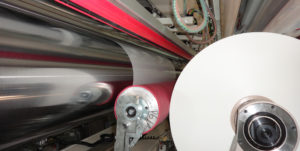
Thickness of Material
For most plastic films, the material is transparent to the charge, so neutralising the charge on one side will neutralise it on the other side. It is possible, however, for an independent charge to exist on both sides of a thicker film. For materials over 5mm you should assume that double-sided neutralisation is required.
Surface or Volumetric Charge
Static is normally a charge on the surface of a material and so relatively easy to neutralise. Sometimes the charge is inside the polymer – for example, due to intense fields produced by corona treating, or the multi-layer nature of some high-tech films. These volumetric charges are more difficult to neutralise. Static neutralisation may be possible only when the charge has had time to migrate to the surface.
Last Updated: 27 November, 2020